Jennifer Rice is waiting for a text message something like this: “Hey, I need the maintenance crew to come out and check this part.”
The sender? A bridge.
Text messages from bridges may seem newfangled, but Rice, a University of Florida structural engineer, says bridges can communicate with humans now via sensors, and in her laboratory she is refining those sensors to better monitor structural health.
“You can envision in the future, at least I can, an interactive system with smart sensors, smart structures that communicate,” says Rice. Ideally, a bridge could “tell” its owner if there’s a problem.
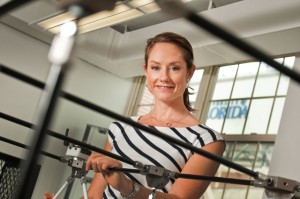
What most bridges might say is that they are worn out. The American Society of Civil Engineers says the average age of U.S. bridges is 42, a ripe old age considering that most existing bridges were designed to last 50 years. More than 30 percent are even older. In its 2013 Report Card for America’s Infrastructure, released in March, the society scored U.S. infrastructure as a whole at D+, with bridges as a category earning a C+.
That means 151,497 bridges, or 25 percent of the bridges in the United States, are either structurally deficient or functionally ob-solete. Every fourth bridge a motorist crosses, on average, could have a problem.
Associate Professor Trey Hamilton, however, says the public mostly does not notice.
“Infrastructure is kind of like the stuff in your house; it becomes a part of the landscape,” says Hamilton, who studies ways to improve bridge construction materials. “You don’t notice until it impedes your day-to-day business.”
Most motorists want one thing from a bridge: to get from one side to the other without incident. Post a bridge with load re-strictions or reduced travel lanes, or close it altogether, and motorists who want to cross it notice.
When a bridge collapses, the world notices.
During the evening rush hour on Aug. 1, 2007, the westbound span of the Interstate 35 bridge over the Mississippi River in Minneapolis fell, killing 13 people. Inspectors had noted problems in preceding years, and in 2001 suggested the bridge be fitted with sensors for continuous structural health monitoring. The bridge was not due for replacement until 2020.
Whether sensors or better materials would have prevented the collapse is a guess, say the two researchers, part of UF’s Engineering School of Sustainable Infrastructure and Environment. Their goal, however, is preventing another bridge failure.
For Rice, sensors are like thermometers for bridges; they give an assessment of condition at a point in time.
“Clearly, there’s an issue with infrastructure. It’s aging beyond its original, intended life, and more than that, we’re using it differ-ently. Our traffic patterns are heavier and trucks are carrying heavier loads,” Rice says.
In her work on structural health monitoring, Rice develops wireless sensors designed to provide data important to protecting public safety and reducing maintenance. Her next-generation sensor fits in the palm of her hand and contains a wireless microprocessor — a tiny computer — that processes data. The sensor has a radio, an accelerometer to measure vibration and a gauge for temperature, hu-midity and light. Placed at the top of a bridge pier, it can detect tilt, which might indicate erosion where the pier is buried. Strain sen-sors can detect localized areas of weakness. Vibration signatures can give an overall reading of a bridge’s stability.
The sensors are designed to collect data and process it on location so that only usable information is transmitted to a remote site, all for around $500 each.
Rice tests the sensors in two laboratories. In Weil Hall, at the Smart Infrastructure Management Laboratory on the main UF cam-pus, Rice fits a 12-foot-long model truss bridge with sensors, then damages it. By taking out a healthy component and replacing it with a damaged component, she can test the algorithms she has developed for detecting damage and the bridge’s response to damage.
The UF East Campus on Waldo Road offers more opportunities to do damage — and tests — at the Powell Family Struc-tures and Materials Laboratory. There, a six-degrees-of-freedom shake table can recreate complex seismic motions, presenting new ways to test how sensors capture data when model structures are damaged or repaired. The shake table, the only one of its kind in Florida, allows for testing smaller subcomponents as well.
“Say you have hundreds of sensors on a bridge, thousands even. With electronics becoming cheaper and cheaper, you could really go to town instrumenting a bridge,” Rice says. “But at the end of the day, what do you want to know? Has the bridge sustained damage, is there a problem, and if so, where?”
A sensor could send an alert — perhaps a text message in the future — and a human would come out to make a visual inspec-tion and decide what needs to be done.
Technology costs are dropping — sensors on the I-35 replacement bridge were just $1 million of the $234-million cost — mak-ing sensors affordable for even a large-scale health assessment of an inventory of bridges, Rice says. Florida, for example, has more than 11,000 bridges, and could get a reading on all of them with a campaign-style approach.
“You’re not going to instrument them all indefinitely, but what if you test a bridge for two weeks, see how it’s doing, pull the sensors off, and go on to the next bridge?” Rice says.
The wireless sensors are so easy to install and uninstall that an inspector could move through many bridges quickly and get an overall picture of the health of bridges region by region. Over time, patterns could emerge in how bridges with common designs perform.
For larger bridges, sensors would be attached and left in place indefinitely, powered by the sun or vibrations. Rice was part of a team collaborating on the largest bridge sensor project in the world in South Korea, where more than 100 sensors were installed in 2009 to monitor the Jindo Bridge. For a while, Rice kept tabs on the bridge from her computer in Gainesville.
For long-term, large-scale deployment, sensors have to be as robust and flexible as possible to overcome the differences in time scale, Rice says. Technology evolves quickly, yearly even, but bridges are built to last 50 years or longer.
“The time scale of technology is so much different from the time scale of what you want to monitor,” Rice says.
Time is an issue for Hamilton, too. Previous design standards called for a 50-year lifespan for a bridge. Today, highway officials are asking for bridges with a service life of 100 years, Hamilton says, and achieving that goal will require more durable materials.
“What do you do to concrete to make it better? What do you do to the reinforcing steel to improve its performance?” Hamilton asks.
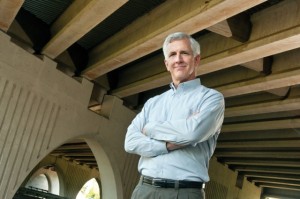
Florida’s bridges got high marks in the infrastructure report, with fewer than 3 percent rated structurally deficient. State Depart-ment of Transportation corrosion engineer Mario Paredes says that is partly due to an aggressive research program in collaboration with UF.
Hamilton is looking at concrete composites that use carbon fibers, glass fibers and polymers to repair corroded bridges and build new ones. Many Florida bridges are close to the Atlantic Ocean or the Gulf of Mexico, so salt water is always a concern.
A standard bridge pier is constructed of concrete around a steel rod. As the concrete wears away, salt water can reach the steel, causing corrosion and eventually weakening the support pier.
“If steel is corroding and concrete is falling off, motorists and pedestrians see this and worry about the structural soundness of the bridge,” Hamilton says. “Corrosion is insidious, degrading the structure’s ability to provide service slowly over time.”
Once salt gets into the concrete, it’s hard to get out. So Hamilton is searching for ways to augment concrete to keep the salt out. The alternative, building with stainless steel, seems like a “no-brainer,” Hamilton says, until you consider the exorbitantly high cost.
When Hamilton finds something that works in the laboratory, he uses a guinea pig bridge to test it in the real world. One in West Florida, a tiny bridge on the Intracoastal Waterway, has been using new materials for five years, with great success. The project used several different materials in the concrete for the piers as part of the federally funded, 10-year-old Innovative Bridge Research and Construction program, which encourages engineers to try new ideas in actual construction, as a test run.
Things that look good in the lab may not translate into practice, Hamilton says. Scientists pay attention to every detail in a lab, but scientists are not the bridge builders in the real world, where construction practices sometimes uncover flaws that did not show up in the lab.
Two bridges repaired with composites will soon provide more ideas for Hamilton. A bridge in Jacksonville and another in Mel-bourne are about to be replaced, and the beams will be examined to see how the repair materials held up.
While a small research bridge is ideal for testing, signature bridges require a different approach, Hamilton says. For a land-mark structure, at least today, concrete and steel is the way to go.
“We have to be sure new materials will work before we build a Skyway with them,” Hamilton says, referring to the Bob Graham Sunshine Skyway Bridge spanning Tampa Bay.
With 100-year lifespans as the new goal, it will be even harder to track how bridges perform with new materials and methods, be-cause they will far outlast the researchers.
“With a bridge, it’s very difficult to extrapolate from the lab to the actual environment,” Hamilton says.
As today’s students become tomorrow’s engineers, Rice thinks sensors will become standard.
“They understand the idea of a ubiquitous sensor network. They say, ‘Of course you’re going to put sensors on a bridge and of course they’re going to communicate wirelessly,’” Rice says. “They get it.”
Collaboration is important, too, Hamilton and Rice emphasize. Rice points out that she’s a structural engineer, but draws on exper-tise from the electrical engineering and computer science departments. Hamilton draws on expertise from colleagues in materials engineering and chemical engineering.
“The typical civil engineering background isn’t enough to solve these problems,” Rice says. “Interesting things kind of happen at the boundaries of the different engineering disciplines.”
Sources:
- Jennifer Rice, Assistant Professor, Engineering School of Sustainable Infrastructure and Environment
- Trey Hamilton, Professor of Electrical and Computer Engineering and Computer Science
Related Website:
Facts About Bridges
- From 1990 to 2007, vehicle travel on Florida’s highways increased 87 percent.
- More than 200 million trips are taken daily across deficient bridges in the nation’s 102 largest metropolitan regions.
- One in nine bridges nationwide is structurally deficient, meaning one or more components have deteriorated.
- The Federal Highway Administration estimates eliminating the nation’s bridge deficit backlog by 2028 would require $20.5 billion annually, while we are spending $12.8 billion currently.
- The 66,749 structurally deficient bridges make up one-third of the total bridge decking in the country, showing that they are significant in size and length.
- Florida is one of five states with less than 5 percent of its bridges rated structurally deficient.
- Florida’s two busiest structurally deficient bridges are the Interstate 95 bridge at State Road 9 in Duval County, carrying an average daily traffic of 172,000, and the northbound Interstate 275 bridge over Tampa Bay, with an average daily traffic of 73,750.
- The Report Card for America’s Infrastructure graded bridges at C- in 1998.
Source:
- The American Society of Civil Engineers Report Card for America’s Infrastructure, March 2013 Transportation for America
This article was originally featured in the Summer 2013 issue of Explore Magazine.