Mat Chandler doesn’t have a magic wand or a vial of pixie dust, but at the intersection of art, science and technology that is the University of Florida Infinity Fab Lab, he conjures up magic all the same.
Chandler is the guiding force behind the Fab Lab, likely the most rampantly creative spot at UF. It’s a place where that idea rolling around in your head takes shape, literally, with a 3-D printer, a laser cutter or the latest addition, a water jet.
The Fab Lab started the fall semester with a new name and a new location in Infinity Hall at Innovation Square. Chandler hopes the vibe from the UF residence hall above, which will house the nation’s first entrepreneurial academic residential community, will also bring added energy.
“There are 308 beds above us filled with innovation, engineering, entrepreneurship; creative-minded kids just ready to do something,” says Chandler. “That’s awesome energy, awesome synergy.”
Even though the Fab Lab is only six years old, it had outgrown its original space in the College of Design, Construction and Planning, a victim of its own success. The lab started as a collaboration between the College of the Arts and the College of Design, Construction and Planning and initially was open only to art and architecture students — hence the old name A2 Fab Lab — when it opened in 2009.
But makers and innovators from other colleges kept finding their way there and asking for advice on projects or to use the 3-D printer or laser cutter or CNC router. To meet that need, the Fab Lab opened in 2012 to all faculty and students and became one of the first university makerspaces in the country to open to the community at large. Last year, Chandler estimates, the lab served more than 2,000 clients.
When approached about a move to Infinity Hall, Chandler jumped at the opportunity because it meant he could add more and newer 3-D printers, including those that print carbon fiber, as well as a water jet that can cut such extreme materials as metal, glass and granite up to six inches thick. The lab also houses a 3-D scanner and a three-axis CNC router.
“The space in Infinity Hall opens up a ton of possibilities for us, and for people who want to create,” says Chandler, noting that it still operates under the auspices of the College of Design, Construction and Planning and the College of the Arts.
Just about anything that can be imagined in digital form can be rendered in physical form. With the help of 2-D and 3-D modeling software, the idea in your head becomes something you can hold in your hand.
The ideas that land on his doorstep often surprise even Chandler, who well understands the creativity the maker machinery unleashes. For example, as an architecture and entrepreneurship graduate himself, Chandler had not given much thought to applying his skills to epilepsy research.
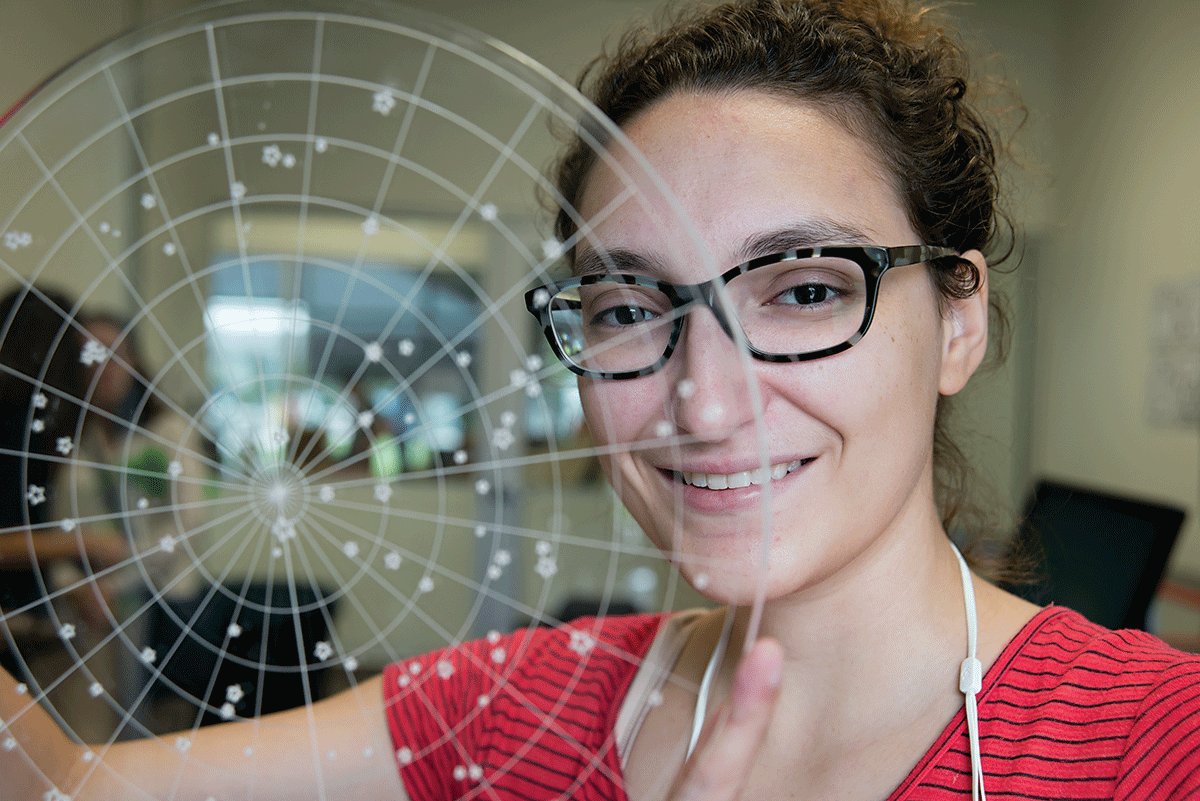
Then doctoral researcher Tao Zhang pinged him with an intriguing idea: Could Chandler help him figure out how to fabricate a skullcap that would allow lab rats to be awake while their brains were imaged to detect the onset of an epileptic seizure?
Chandler didn’t know, but figured it was worth a try. He walked down the hill to Zhang’s biomedical engineering lab to check out the project and decided he could use a 3-D scanner to scan the heads of rats and turn the scan into a model that could be used to print a cap.
Zhang said the 3-D printed skullcaps solved one of the challenges of his study: how to use a larger number of fiber bundles and still keep the rats comfortable during the experiments. Previously, researchers had to surgically implant fibers for imaging the rats’ skulls, but that limited them to 10 fibers and required anesthesia that left the rats groggy.
“With the 3-D printed interface, we were able to place 30 fiber bundles onto the rats’ skulls while they were awake, and the more fiber bundles we use, the more information we can collect from the rats’ brains,” says Zhang, whose article on the research was printed in The Journal of Neuroscience Methods earlier this year.
Zhang says he knows of other locations on campus to access 3-D printers, but he knows of nowhere else that he could have tapped into 3-D modeling and printing expertise.
“When I started I had no idea how to do 3-D modeling or printing,” Zhang says. “They were the experts, they provided training, and they were there if I had questions.”
Chandler acknowledges that 3-D printers are common across campus, but some are proprietary — part of a particular lab — and some are set up for use by people who already know how to use the machines. The other labs send would-be inventors to the Fab Lab if they need help or need a high-end $120,000 3-D printer that uses multiple materials. And no place on campus has the collective machinery of invention amassed at the Infinity Fab Lab.
Another huge benefit of the Fab Lab is its 24-7 laser-cutting schedule, and that is a key to keeping it accessible to the students whose work it was originally intended to support. Creativity is not a 9-to-5 endeavor, and the art and architecture students, Chandler says, are more likely to show up in the wee hours, especially 4 a.m., which Chandler calls “the special hour.”
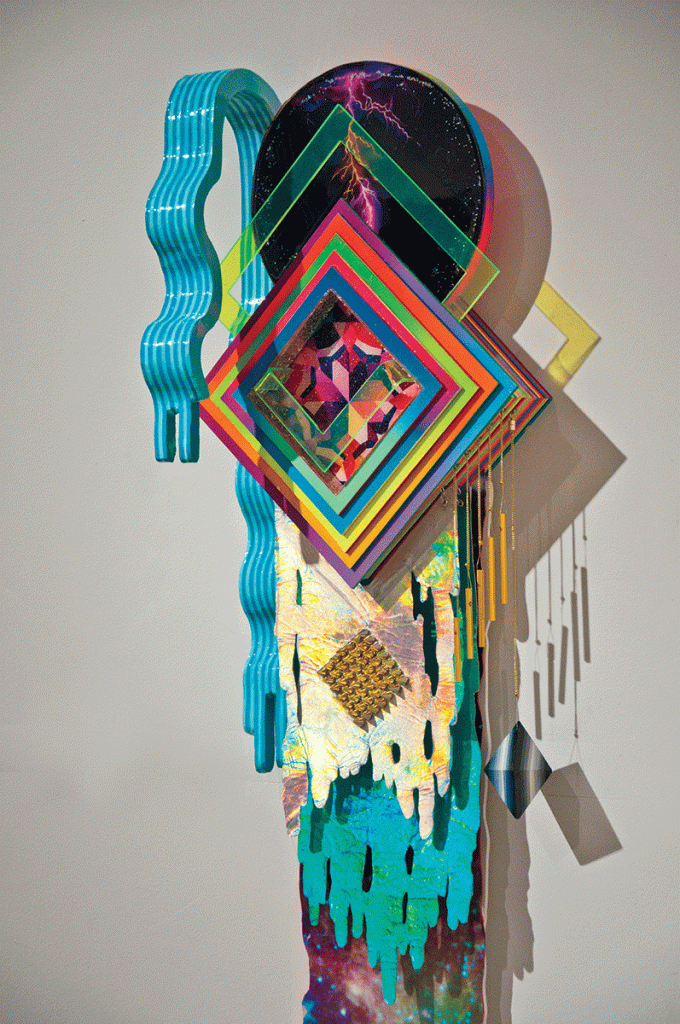
Art student Hilary White said the Fab Lab was the first thing she wanted to learn about when she arrived at UF in 2013. White creates 3-D multimedia installations full of color and movement and has exhibited nationally and internationally. The Fab Lab — especially the laser cutter — expedites her vision, she says.
“With the Fab Lab, it’s a quicker way to realize an idea,” White says.
White says when she cuts by hand it can take two or three months to finish a piece. That takes time and money, and if the end product is not satisfactory, it’s time and money wasted.
“This allows me to build smarter and better. I can visualize something virtually before creating it,” White says. The off hours at the lab offer quiet and the ability to concentrate, and she says she has run into architecture students, too, at those hours.
“The fact that it’s 24 hours is incredible,” White says. “It’s such a gift to have accessibility to these tools 24 hours a day. I’m excited that it’s growing, and I think it will become more and more of a hub.”
Chandler says some of the architecture models produced today at the Fab Lab would not have been possible at all without it. Architecture students can build small pavilions at 1-to-1 scale rather than just models, venture into furniture making and even cast new shapes and test materials in CNC (computer numerical control) created formwork.
The lab keeps a shelf of prototypes on display, and they tell a story that ranges from whimsical — a 3-D printed mask of Chandler’s face, for instance — to conventional — a valve prototype that turns ordinary Ziploc bags into vacuum bags. A local resident once asked if he could replicate antique croquet balls, hundreds of years old. He could. A kid came in to fabricate a gift for his dad. Professors of all disciplines have walked in.
For researchers on limited funding, bringing down the cost of prototyping is a huge benefit, and even a key to landing future grants.
UF physiology Professor Paul Davenport, who studies the science of respiration, says he is one of the Fab Lab’s biggest fans. He used the Fab Lab to prototype an idea that had been nagging him since 1982, when he worked on his first grant at the University of Florida.
Davenport’s goal was a device that does two things. First, it uses sound waves to break up pulmonary congestion, such as the mucus buildup experienced by a cystic fibrosis patient. Second, it collects molecules from deep airways to help with diagnosis of lung ailments.
For 30 years, the project sat to the side. Then he had the idea to try to use sound waves to vibrate airways internally and returned to his original idea. He went to Best Buy to get a guitar amplifier, then to Lowe’s for PVC pipe. He connected them to a wave form generator and experimented to see which kind of sound waves broke up mucus and produced exhaled air full of molecules.
“So it worked,” Davenport says, but the contraption was clunky, and he knew a manufacturer would be skeptical.
“It quickly became very clear that a company was not going to buy a guitar amplifier connected to a piece of PVC pipe,” Davenport said.
He began sketching the device he imagined, but hesitated to invest $1,500 to get it produced, knowing he would want to adjust it many times— at thousands and thousands of dollars more — before arriving at a final design. That’s when a colleague mentioned the Fab Lab.
Davenport says Chandler was able to translate his amateur drawing into something that could be modeled and printed, and he did it with Davenport by his side. They printed a device, and modified each successive design until they arrived at a final product. At a machine shop, that process would take weeks or months — perhaps longer — and cost tens of thousands of dollars. The Fab Lab was a fraction of that cost, and faster, and resulted in a better device.
Davenport says the low cost is a key for advancing science. Prototypes, he says, often are necessary to show proof of concept in winning a grant, and most researchers use money they have scrimped and saved to produce prototypes. An inexpensive prototype is the key to getting from idea to grant. Today, a patent is pending on the device Davenport developed at the Fab Lab.
“In the old days, I actually learned how to work lathes and drill presses and that sort of thing to make my own devices,” Davenport says. “The Fab Lab is like a gadget guy’s heaven, because now all I have to do is draw it. I still have gadgets I was making back in the late 1970s, more designs to try.”
The lab operates on a membership model, with students charged the lowest fees and faculty a little more. Community members pay a higher fee because an intern or a member of the Student Design Team is assigned to help them with their projects. That helps students because they get a chance to flex their skills and learn how to interface with a customer, and it helps the customers because they are paying a quarter to half what they’d pay anywhere else.
“We’re the intermediary between manufacturing and the garage setup,” Chandler says. “We love projects that help people.”
Chandler says the tools of creation available at the Fab Lab unlock the potential inside people who think they can’t draw or can’t cut a straight line. Making the machinery accessible puts art and science into motion, Chandler says.
“This allows people to create who never thought they could,” Chandler says. “That’s what makes me love this place the most, the creativity that comes out of here. Every day somebody surprises me with something.”
Related Website:
This article was originally featured in the Fall 2015 issue of Explore Magazine.