In retrospect, chemist Brent Sumerlin says, landing at the University of Florida in the Butler Lab seems like destiny.
The lab is named for UF Professor George Butler, one of the pioneers in polymer chemistry from his arrival at UF in 1946 until his death in 2007. Butler was possibly the first UF researcher to receive an external grant and, it turns out, the Johnny Appleseed of polymer chemistry.
“George Butler was the Ph.D. adviser of my Ph.D. adviser, and the postdoc adviser of my postdoc adviser,” says Sumerlin, now the George B. Butler Professor of Polymer Chemistry in the George & Josephine Butler Polymer Research Laboratory.
“Coming to UF was in my bloodline.”
Although Butler was the lone polymer chemist on campus until 1972, polymer chemistry is now one of the largest research enterprises on campus. If you walk the third floors of Leigh and Sisler Halls, you pass hallways of doors labeled Butler Polymer Chemistry Laboratory. Including faculty, postdocs, graduate students and undergraduate researchers, more than 100 minds are engaged in polymer research. Most chemistry departments have one polymer chemist, if that, Sumerlin says, making UF’s concentration in polymer chemistry stand out.
Over the course of his 50-year UF career, Butler mentored more than 200 graduate students, many of whom went on to mentor their own students or to successful careers in industry. The field of polymer chemistry — at UF and beyond — owes a chunk of its foundation to Butler.
While UF’s polymer chemists honor tradition, they don’t stand still, says Sumerlin, who last year took the reins from longtime Butler Professor Ken Wagener, who has mentored 159 students of his own. Recently, Sumerlin says, polymer chemistry has matured.
“For years, polymer chemistry was looked down on as too applied,” Sumerlin says. “Today, it’s more elegant; less about making paint in a bucket and more about making well-defined polymers that mimic proteins or DNA that can store information in a molecule.
“The fact that you can make materials for defense applications, to treat disease, has led to more funding and more hiring,” Sumerlin says. “Polymer chemists today play a huge role in biomedicine and energy.”
The Chain
Polymers can be natural, like proteins, or synthetic, like plastic for a milk jug. At first glance, they seem simple: take many single molecules, or monomers, and connect them, and you get a polymer. In principle, any monomer that will bind with another monomer can be made into a polymer, changing into something entirely new.
But a chain is only one form a polymer can take. Monomers can bind together in more intricate ways, creating more complex architectures, and discovering applications for these new polymers is one of the intriguing things about his work, Sumerlin says.
“Since we’re a synthetic group, we make new, sometimes exotic, macromolecules. We don’t always have an intended application for what we synthesize, but we make it and publish it,” Sumerlin says. “It’s like ‘If you build it they will come,’ only it’s ‘If you publish, people will seek your help.’ That happens a bunch.”
That happened on campus with the Soft Matter Engineering Group, which 3-D prints the softest materials in hydrogel. Printing tubes, a technique that would be useful for printing synthetic blood vessels, for example, proved tricky. The soft, flexible tubes could be printed, but they came out filled with hydrogel, not hollow, and removing the hydrogel was not easy.
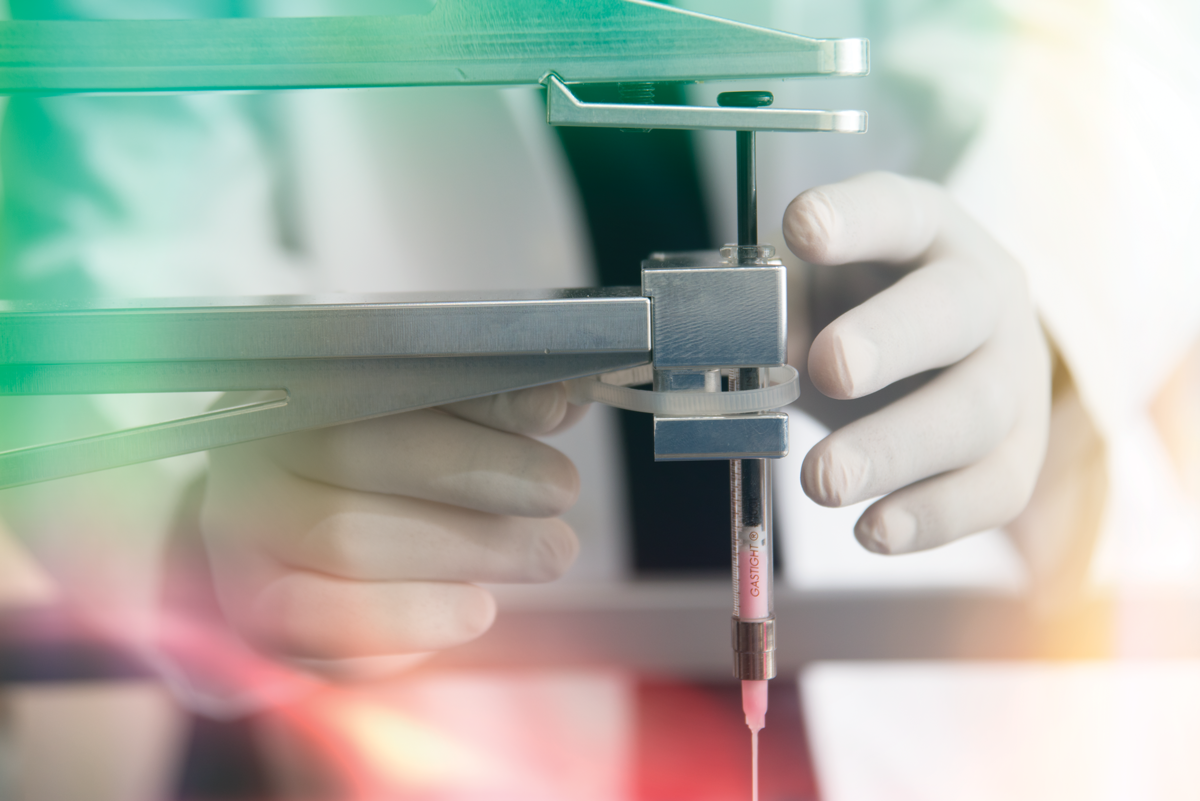
The engineers, W. Gregory Sawyer and Tommy Angelini, called Sumerlin after seeing his work in a journal, and explained the problem.
“We created a polymer to print inside the tube,” Sumerlin says, “and it dissolves when you shine a light on it, so the tube filling slides right out.”
Collaboration comes naturally in polymer chemistry with fields such as materials science, biomedicine, and chemical and mechanical engineering, Sumerlin says. Lately, his group has worked on biological applications of polymers for drug delivery.
With colleague Carlos Rinaldi, chemical engineering department chair, Sumerlin’s group is creating nanoparticles made of polymers that respond to something going on around them, perhaps a biological cue, such as the reduced pH of a tumor environment or the application of a magnetic field. In that instance, a solution of magnetic nanoparticles carrying an anti-cancer drug could be injected, circulate until the nanoparticles recognize the tumor, then accumulate. Then a magnetic field could be applied, which would heat up the magnetic nanoparticles, breaking the bonds that attach the drugs to the particles and releasing the drug into the tumor, sparing the nearby healthy tissue.
In another project, in mice, Sumerlin’s group made synthetic polymers and attached them to a protein called osteoprotegerin, which can be used to treat a variety of degenerative bone disorders, including osteoporosis. Injections of osteoprotegerin could help, but the protein only circulates for minutes, limiting its therapeutic value. To prolong circulation, Sumerlin attaches a polymer to it, which enlarges the protein so that it cannot easily fit through the pores in the kidneys. That allows it to circulate longer before it is excreted.
Shape Matters, Too
“One of the things my group does is we make what you might call exotic polymers,” Sumerlin says. “They have well-defined architectures. It doesn’t have to be just a linear chain, it can be branched, it can have branches upon branches, tree-like, comb-like. We look at the effect of the polymer shape on biological properties.”
In mice, one particular shape of polymer performed better at promoting higher bone mineral density when attached to osteoprotegerin. That was not what team members expected, however, so now they are investigating why it works. Computational chemist Coray Colina, also in the Butler Lab, is modeling how the protein is affected by an attached polymer.
“We hope to be able to determine why this shape works best,” Sumerlin says. “Maybe we can make it better.”
Colina’s computational modeling can be a guide to synthesize specific polymers for a wide variety of proteins, Sumerlin says.
In work in diabetes, Sumerlin’s group is making polymeric vesicles — tiny, nano-sized balloons roughly 100 nanometers in diameter — filled with insulin. The vesicles circulate in the bloodstream, at the ready, and when they come into contact with a high concentration of glucose, the vesicles dissolve, releasing insulin the way the pancreas would in a healthy person.
The work on glucose in the circulatory system turned out to have applications for citrus greening.
The bacteria that cause greening grow in the phloem, part of the circulatory system for a tree. The bacteria block the arteries, so to speak, which leads to fruit drop and dying trees. With a grant from the Citrus Research Board, Sumerlin is working with collaborators in the Institute of Food and Agricultural Sciences to try nanomedicine on citrus trees. His group has designed polymers to carry an antibiotic to kill the bacteria, after which, the polymers degrade into harmless amino acids.
Sumerlin got word of the greening project by happenstance. An IFAS researcher emailed materials science Associate Professor Jennifer Andrew, asking if she could make a soft nanoparticle to help in citrus greening. She forwarded the email to Sumerlin, saying, “This sounds like something you do.”
That email opened the door to agricultural applications of polymers, a field Sumerlin’s group plans to explore further.
Other applications of polymers are not biological, but seem almost space-age. Sumerlin’s group has used polymers to make coatings that are self-healing. After a scratch or a break, they mend themselves. Such polymers could be useful on a large scale in infrastructure, as in a pipe that can mend its own leak, or commercially, in the clear coat on a car.
“There’s a huge push for clear coats that heal themselves, in response to heat or UV light,” Sumerlin says. “Your car door could be scratched while you’re in Publix, and you come outside and the sunlight has already healed it. You don’t even know it happened.
“We’re developing the fundamental chemistry that would allow these polymers to mend themselves, and do it over and over, in the exact same area,” Sumerlin says.
Chemistry and the Environment
A lot of people, when they think about polymers, think plastics: polyethylene, polypropylene, polyolefin, polystyrene. If a period in history is defined by a material — the Stone Age or the Iron Age, for instance — then this is the Plastic Age.
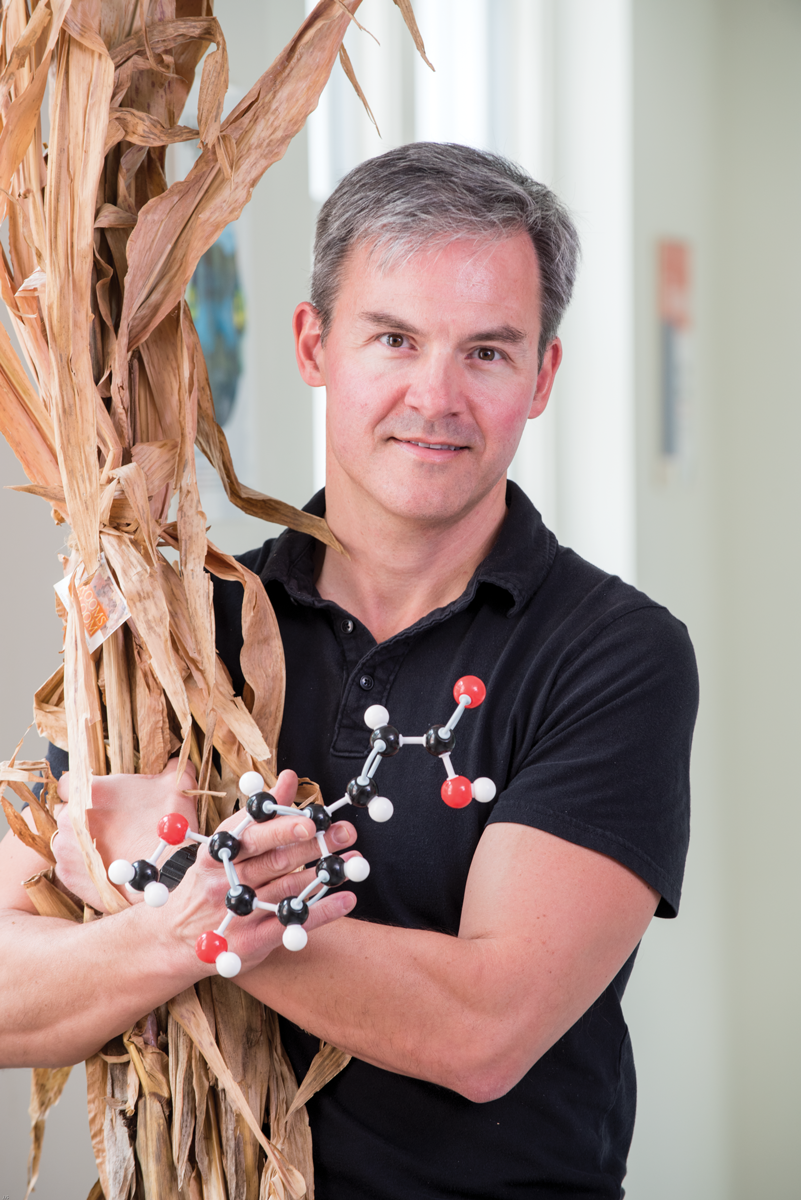
Once hailed as a crowning achievement of polymer chemistry, plastic is now the object of a concerted research effort to get rid of it. Or at least reinvent it. One of its re-inventors is Associate Professor Stephen Miller.
In his office, on a shelf, Miller has a collection of trash: yogurt cups, straws, drink cups of all sizes, safety seals from food packages, cups, mini drink jugs.
“We want to replace these things,” Miller says, grabbing a plastic drink cup.
The vast majority of plastics originate with fossil fuels, so he’s looking for a way to make them from a renewable resource, like plants. Not only that, but he wants to make them degrade when they end up on a roadside, in an ocean, or in a landfill.
“Green birth, green death,” Miller says.
Miller says only 11 percent of plastic is recycled, and one study shows that half of all plastic manufactured becomes trash in less than a year. If plastics degrade, however, recycling would be less urgent.
The number one polymer in terms of manufacturing is polyethylene, Miller says. We know it as a milk jug, a Ziploc bag or a grocery bag. Polyethylene lasts about 1,000 years in the environment.
Another common plastic is polypropylene.
“Virtually every yogurt cup or water bottle cap on earth is polypropylene,” Miller says.
Miller’s group is looking at plant-based raw materials for plastic production, such as corn starch and sugar cane waste. The challenge is to produce a plastic that is structurally sound for as long as it needs to hold a food or a liquid, yet easily degradable when its usefulness has passed. Competing interests, so to speak.
The other challenge is cost. Today’s commodity plastics have been optimized for manufacturing because chemists have been working with them since the 1920s or so. Newer, greener plastics do not have that long history.
“As a chemist, I approach this from a molecular standpoint. We think about molecules nature will give us, that have to be abundant and have to be cheap. If you can’t make them abundantly and cheaply you’re never going to compete with a water bottle that costs a penny to make today,” Miller says.
One plastic in development is on his shelf. It looks like the plastic in a water bottle, but it’s polylactic acid, or PLA, made from corn. It’s commercially available, but has major limitations. A typical water bottle costs a penny, this one costs 1.25 pennies, a drop from decades ago when the markup was 10 to 15 times higher.
Its other limitation is thermal resistance. For cold substances, it’s fine, but high temperatures start the process of deformation.
“If you put a cup of coffee in this at 62 degrees Celsius, it will turn into a wet noodle,” Miller says.
While PLA is marketed as compostable, Miller says he has a couple of cups in his back yard that he has been keeping an eye on for three years. “They still look like cups.”
Some polymers have been developed that degrade in humid air, so they would not last a long time in the environment, but they also could not be used for items that need a long shelf life. Tossed into water, they degrade in about a year. Miller sees a market for this plastic in wrappings for non-food products, like batteries.
Plastics made from corn or other plant materials degrade into smaller pieces, which become food for microbes, and then turn back into carbon dioxide, which plants then use to grow. It’s a natural, closed-loop cycle, unlike polyethylene — the milk jug — that degrades on a geologic time scale. With green plastics, the Earth’s plastic trash burden stops growing, Miller says.
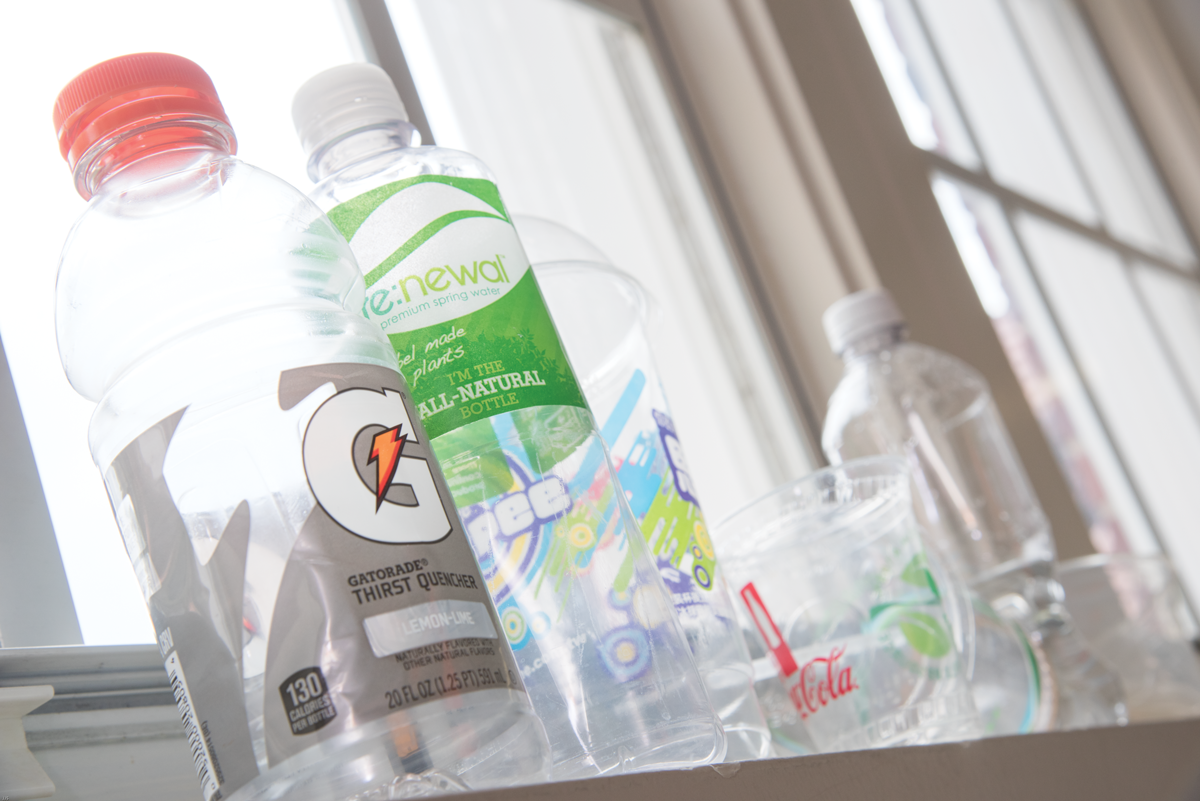
“The idea is to put X amount of plastic into the environment, at the same time X amount disintegrates,” Miller says.
Miller’s lab recently phased out all its petroleum-based plastics projects.
“The National Science Foundation wants the next new thing, not something that looks like what we were doing in the 1950s,” Miller says.
Paradoxically, the largest manufacturers are not yet on board. In communications with one, Miller got back a letter saying the company was not interested in new-to-the-world polymers. Another large retailer said it wanted a plastic made with a technology that only it could use.
“They wanted to save the planet, but wouldn’t let anyone else in on the secret,” Miller says. “And we’re not making train cars full of that magic polymer in the lab anyway.”
Miller recently was part of a team awarded a $15 million grant from the USDA. The large consortium, centered at UF, is called the Southeast Partnership for Advanced Renewables from Carinata, or SPARC. While the main goal of the project is to use carinata seed oil for jet fuel, the plant byproducts can be used to make plastics.
With carinata, as with corn, the raw material for future plastics is abundant.
“We need to find out what nature is going to give us in large quantity, and then figure out chemistries, new chemistries, adaptive chemistries, to make polymers and study their properties,” Miller says. “There is no super polymer out there.”
Yet.
Sources:
- Brent Sumerlin, Professor of Chemistry
- Stephen Miller, Associate Professor of Chemistry
- Kevin Folta, Professor and Chairman, Department of Horticultural Sciences
Related Website:
This article was originally featured in the Spring 2018 issue of Explore Magazine.